Ang porosity, mga cavity-type na discontinuities na nabuo sa pamamagitan ng gas entrapment sa panahon ng solidification, ay isang pangkaraniwan ngunit masalimuot na depekto sa MIG welding at isa na may iba't ibang dahilan. Maaari itong lumabas sa mga semi-awtomatikong o robotic na application at nangangailangan ng pag-alis at muling paggawa sa parehong mga kaso — humahantong sa downtime at pagtaas ng mga gastos.
Ang pangunahing sanhi ng porosity sa welding ng bakal ay nitrogen (N2), na nasangkot sa welding pool. Kapag lumamig ang likidong pool, ang solubility ng N2 ay makabuluhang nabawasan at ang N2 ay lumalabas sa tinunaw na bakal, na bumubuo ng mga bula (pores). Sa galvanized/galvanneal welding, ang evaporated zinc ay maaaring haluin sa welding pool, at kung walang sapat na oras upang makatakas bago ang pool ay tumigas, ito ay bumubuo ng porosity. Para sa hinang ng aluminyo, ang lahat ng porosity ay sanhi ng hydrogen (H2), sa parehong paraan kung paano gumagana ang N2 sa bakal.
Ang welding porosity ay maaaring lumabas sa labas o panloob (madalas na tinatawag na sub-surface porosity). Maaari rin itong bumuo sa isang punto sa hinang o sa buong haba, na nagreresulta sa mahinang mga hinang.
Ang pag-alam kung paano tukuyin ang ilang pangunahing sanhi ng porosity at kung paano mabilis na malutas ang mga ito ay maaaring makatulong sa pagpapabuti ng kalidad, produktibidad at ang bottom line.
Mahina ang Covering Gas Coverage
Ang mahinang shielding gas coverage ay ang pinakakaraniwang dahilan ng welding porosity, dahil pinapayagan nito ang mga atmospheric gases (N2 at H2) na mahawahan ang weld pool. Maaaring mangyari ang kakulangan ng wastong saklaw sa ilang kadahilanan, kabilang ang ngunit hindi limitado sa mahinang shielding gas flow rate, pagtagas sa channel ng gas, o sobrang daloy ng hangin sa weld cell. Ang bilis ng paglalakbay na masyadong mabilis ay maaari ding maging salarin.
Kung pinaghihinalaan ng isang operator ang mahinang daloy ang sanhi ng problema, subukang ayusin ang gas flow meter upang matiyak na sapat ang rate. Kapag gumagamit ng spray transfer mode, halimbawa, ang 35 hanggang 50 cubic feet per hour (cfh) na daloy ay dapat sapat na. Ang welding sa mas mataas na mga amperage ay nangangailangan ng pagtaas sa daloy ng rate, ngunit mahalagang huwag itakda ang rate ng masyadong mataas. Maaari itong magresulta sa kaguluhan sa ilang disenyo ng baril na nakakaabala sa pagsaklaw ng gas.
Mahalagang tandaan na ang mga baril na may iba't ibang disenyo ay may iba't ibang katangian ng daloy ng gas (tingnan ang dalawang halimbawa sa ibaba). Ang "sweet spot" ng rate ng daloy ng gas para sa tuktok na disenyo ay mas malaki kaysa sa disenyo sa ibaba. Ito ay isang bagay na kailangang isaalang-alang ng welding engineer kapag nagse-set up ng weld cell.
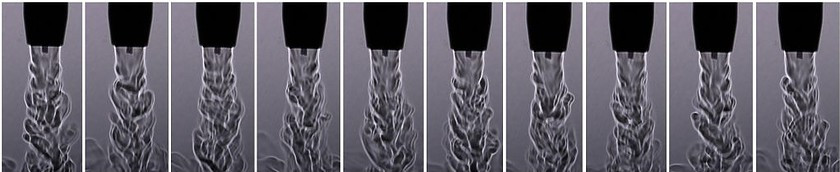
Ang disenyo 1 ay nagpapakita ng makinis na daloy ng gas sa labasan ng nozzle
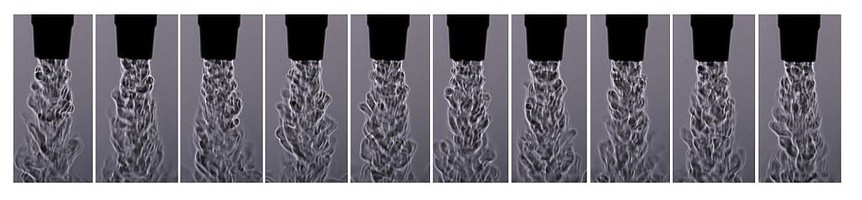
Ang disenyo 2 ay nagpapakita ng magulong daloy ng gas sa labasan ng nozzle.
Suriin din kung may pinsala sa gas hose, fitting at connectors, pati na rin ang mga O-ring sa power pin ng MIG welding gun. Palitan kung kinakailangan.
Kapag gumagamit ng mga bentilador upang palamig ang mga operator o mga bahagi sa isang weld cell, mag-ingat na ang mga ito ay hindi direktang nakatutok sa lugar ng hinang kung saan maaari silang makagambala sa saklaw ng gas. Maglagay ng screen sa weld cell upang maprotektahan mula sa panlabas na daloy ng hangin.
Pindutin muli ang program sa mga robotic na application upang matiyak na mayroong tamang distansya sa tip-to-work, na karaniwang ½ hanggang 3/4 pulgada, depende sa gustong haba ng arko.
Panghuli, mabagal ang bilis ng paglalakbay kung magpapatuloy ang porosity o kumunsulta sa isang supplier ng MIG gun para sa iba't ibang front-end na bahagi na may mas magandang gas coverag
Base Metal Contamination
Ang base metal contamination ay isa pang dahilan kung bakit nangyayari ang porosity — mula sa langis at grasa hanggang sa mill scale at kalawang. Ang kahalumigmigan ay maaari ring hikayatin ang hindi pagkakatuloy na ito, lalo na sa aluminum welding. Ang mga uri ng contaminant na ito ay karaniwang humahantong sa panlabas na porosity na nakikita ng operator. Ang galvanized na bakal ay mas madaling kapitan ng subsurface porosity.
Upang labanan ang panlabas na porosity, tiyaking linisin nang lubusan ang base material bago ang welding at isaalang-alang ang paggamit ng metal-cored welding wire. Ang ganitong uri ng wire ay may mas mataas na antas ng mga deoxidizer kaysa sa solid wire, kaya mas mapagparaya ito sa anumang natitirang mga contaminant sa base material. Palaging itabi ang mga ito at anumang iba pang mga wire sa isang tuyo, malinis na lugar na katulad o bahagyang mas mataas ang temperatura kaysa sa halaman. Ang paggawa nito ay makakatulong na mabawasan ang condensation na maaaring magpasok ng moisture sa weld pool at magdulot ng porosity. Huwag mag-imbak ng mga wire sa isang malamig na bodega o sa labas.
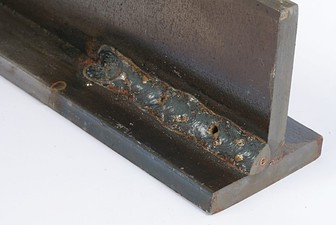
Ang porosity, mga cavity-type na discontinuities na nabuo sa pamamagitan ng gas entrapment sa panahon ng solidification, ay isang pangkaraniwan ngunit masalimuot na depekto sa MIG welding at isa na may iba't ibang dahilan.
Kapag nagwe-welding ng galvanized steel, ang zinc ay umuusok sa mas mababang temperatura kaysa sa natutunaw na bakal, at ang mabilis na bilis ng paglalakbay ay may posibilidad na mabilis na mag-freeze ang weld pool. Maaari nitong ma-trap ang zinc vapor sa bakal, na nagreresulta sa porosity. Labanan ang sitwasyong ito sa pamamagitan ng pagsubaybay sa bilis ng paglalakbay. Muli, isaalang-alang ang espesyal na dinisenyo (flux formula) metal-cored wire na nagtataguyod ng zinc vapor escape mula sa welding pool.
Barado at/o Maliit na Laki na Mga Nozzle
Ang barado at/o maliit na laki ng mga nozzle ay maaari ding magdulot ng porosity. Ang welding spatter ay maaaring mabuo sa nozzle at sa ibabaw ng contact tip at diffuser na humahantong sa restricting shielding gas flow o nagiging sanhi ito upang maging magulong. Ang parehong mga sitwasyon ay umalis sa weld pool na may hindi sapat na proteksyon.
Ang pagsasama-sama ng sitwasyong ito ay isang nozzle na masyadong maliit para sa aplikasyon at mas madaling kapitan ng mas malaki at mas mabilis na spatter buildup. Ang mas maliliit na nozzle ay makakapagbigay ng mas magandang joint access, ngunit nakakasagabal din sa daloy ng gas dahil sa mas maliit na cross-sectional area na pinapayagan para sa daloy ng gas. Palaging tandaan ang variable ng contact tip sa nozzle stickout (o recess), dahil ito ay maaaring isa pang salik na nakakaapekto sa pagprotekta sa daloy ng gas at porosity sa iyong pagpili ng nozzle.
Sa pag-iisip na iyon, siguraduhin na ang nozzle ay sapat na malaki para sa aplikasyon. Kadalasan, ang mga application na may mataas na welding current na gumagamit ng mas malalaking sukat ng wire ay nangangailangan ng nozzle na may mas malalaking sukat ng bore.
Sa semi-awtomatikong welding application, pana-panahong suriin kung may welding spatter sa nozzle at tanggalin gamit ang welder's pliers (welpers) o palitan ang nozzle kung kinakailangan. Sa panahon ng inspeksyon na ito, kumpirmahin na ang contact tip ay nasa mabuting kalagayan at ang gas diffuser ay may malinaw na gas port. Ang mga operator ay maaari ding gumamit ng anti-spatter compound, ngunit dapat silang mag-ingat na huwag isawsaw ang nozzle sa compound nang masyadong malayo o masyadong mahaba, dahil ang sobrang dami ng compound ay maaaring mahawahan ang shielding gas at makapinsala sa nozzle insulation.
Sa isang robotic welding operation, mamuhunan sa isang nozzle cleaning station o reamer upang labanan ang pagkakaroon ng spatter. Nililinis ng peripheral na ito ang nozzle at diffuser sa mga nakagawiang paghinto sa produksyon upang hindi ito makaapekto sa cycle time. Ang mga istasyon ng paglilinis ng nozzle ay inilaan upang gumana kasabay ng isang anti-spatter sprayer, na naglalagay ng manipis na coat ng compound sa mga bahagi sa harap. Masyadong marami o masyadong maliit na anti-spatter fluid ay maaaring magresulta sa karagdagang porosity. Ang pagdaragdag ng sabog ng hangin sa isang proseso ng paglilinis ng nozzle ay maaari ding makatulong sa pag-alis ng maluwag na spatter mula sa mga consumable.
Pagpapanatili ng kalidad at pagiging produktibo
Sa pamamagitan ng pag-iingat upang subaybayan ang proseso ng hinang at pag-alam sa mga sanhi ng porosity, medyo simple ang pagpapatupad ng mga solusyon. Makakatulong ang paggawa nito na matiyak ang mas malaking arc-on time, kalidad ng mga resulta at mas magagandang bahagi na gumagalaw sa produksyon.
Oras ng pag-post: Peb-02-2020