Ang MIG welding, tulad ng anumang iba pang proseso, ay nangangailangan ng pagsasanay upang pinuhin ang iyong mga kasanayan. Para sa mga mas bago dito, ang pagbuo ng ilang pangunahing kaalaman ay maaaring magdala ng iyong MIG welding operation sa susunod na antas. O kung matagal ka nang nagwe-welding, hindi masakit na magkaroon ng refresher. Isaalang-alang ang mga madalas itanong na ito, kasama ang kanilang mga sagot, bilang mga tip sa welding na gagabay sa iyo.
1. Anong drive roll ang dapat kong gamitin, at paano ko itatakda ang tensyon?
Tinutukoy ng laki at uri ng welding wire ang drive roll para makakuha ng makinis, pare-parehong wire feeding. Mayroong tatlong karaniwang mga pagpipilian: V-knurled, U-groove at V-groove.
Ipares ang gas- o self-shielded wires sa V-knurled drive rolls. Ang mga welding wire na ito ay malambot dahil sa kanilang tubular na disenyo; kinukuha ng mga ngipin sa drive roll ang wire at itinutulak ito sa feeder drive. Gumamit ng U-groove drive roll para sa pagpapakain ng aluminum welding wire. Ang hugis ng mga drive roll na ito ay pumipigil sa pagsira ng malambot na wire na ito. Ang mga V-groove drive roll ay ang pinakamahusay na pagpipilian para sa solid wire.
Para itakda ang tensyon ng drive roll, bitawan muna ang mga drive roll. Dahan-dahang taasan ang tensyon habang pinapakain ang wire sa iyong naka-glove na kamay. Magpatuloy hanggang sa ang pag-igting ay isang kalahating pagliko lampas sa pagkadulas ng wire. Sa panahon ng proseso, panatilihing tuwid ang baril hangga't maaari upang maiwasan ang pagkirot ng cable, na maaaring humantong sa hindi magandang pagpapakain ng wire.

Ang pagsunod sa ilang pangunahing pinakamahuhusay na kagawian na nauugnay sa welding wire, drive roll at shielding gas ay makakatulong na matiyak ang magagandang resulta sa proseso ng MIG welding.
2. Paano ko makukuha ang pinakamahusay na mga resulta mula sa aking MIG welding wire?
Ang mga welding wire ng MIG ay nag-iiba sa kanilang mga katangian at mga parameter ng hinang. Palaging suriin ang spec o data sheet ng wire upang matukoy kung anong amperage, boltahe at bilis ng feed ng wire ang inirerekomenda ng tagagawa ng filler metal. Ang mga spec sheet ay karaniwang ipinapadala kasama ang welding wire, o maaari mong i-download ang mga ito mula sa website ng tagagawa ng filler metal. Ang mga sheet na ito ay nagbibigay din ng shielding gas na kinakailangan, pati na rin ang contact-to-work distance (CTWD) at welding wire extension o mga rekomendasyon sa stickout.
Ang stickout ay lalong mahalaga sa pagkakaroon ng pinakamainam na resulta. Ang masyadong mahaba ng isang stickout ay lumilikha ng mas malamig na weld, bumababa sa amperage at binabawasan ang joint penetration. Ang isang mas maikling stickout ay karaniwang nagbibigay ng isang mas matatag na arko at mas mahusay na mababang boltahe na penetration. Bilang isang patakaran ng hinlalaki, ang pinakamahusay na haba ng stickout ay ang pinakamaikling pinapayagan para sa aplikasyon.
Ang wastong welding wire storage at handling ay kritikal din sa magandang resulta ng MIG welding. Panatilihin ang spool sa isang tuyong lugar, dahil ang kahalumigmigan ay maaaring makapinsala sa wire at potensyal na humantong sa hydrogen-induced crack. Gumamit ng guwantes kapag hinahawakan ang wire upang maprotektahan ito mula sa kahalumigmigan o dumi mula sa iyong mga kamay. Kung ang wire ay nasa wire feeder, ngunit hindi ginagamit, takpan ang spool o alisin ito at ilagay ito sa isang malinis na plastic bag.
3. Anong contact recess ang dapat kong gamitin?
Ang contact tip recess, o ang posisyon ng contact tip sa loob ng MIG welding nozzle, ay depende sa welding mode, welding wire, application at shielding gas na iyong ginagamit. Sa pangkalahatan, habang tumataas ang kasalukuyang, dapat ding tumaas ang contact tip recess. Narito ang ilang rekomendasyon.
Ang isang 1/8- o 1/4-inch recess ay mahusay na gumagana para sa welding sa higit sa 200 amps sa spray o high-current pulse welding, kapag gumagamit ng metal-cored wire at argon-rich shielding gases. Maaari kang gumamit ng wire stickout na 1/2 hanggang 3/4 inches sa mga sitwasyong ito.
Panatilihing flush ang iyong contact tip gamit ang nozzle kapag nagwe-welding ng mas mababa sa 200 amps sa short circuit o low-current pulse mode. Inirerekomenda ang 1/4- hanggang 1/2-inch wire stickout. Sa 1/4-inch stick out sa short circuit, partikular, ay nagbibigay-daan sa iyo na magwelding sa mas manipis na mga materyales na may mas kaunting panganib ng burn-through o warping.
Kapag nagwe-welding ng mga hard-to-reach joint at mas mababa sa 200 amps, maaari mong i-extend ang contact tip 1/8 inch mula sa nozzle at gumamit ng 1/4-inch stickout. Nagbibigay-daan ang configuration na ito ng mas malawak na access sa mga mahirap na i-access na joints, at gumagana nang maayos para sa short circuit o low-current pulse mode.
Tandaan, ang tamang recess ay susi sa pagbabawas ng pagkakataon para sa porosity, hindi sapat na penetration at burn-through at upang mabawasan ang spatter.
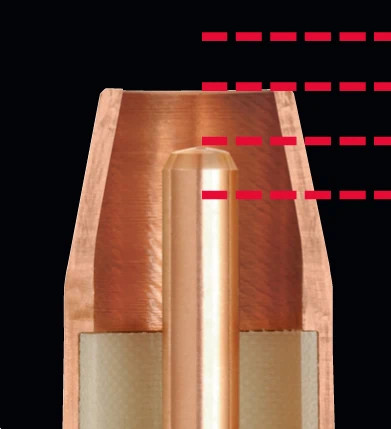
Ang perpektong posisyon ng recess tip sa contact ay nag-iiba ayon sa aplikasyon. Isang pangkalahatang tuntunin: Habang tumataas ang kasalukuyang, dapat ding tumaas ang recess.
4. Anong shielding gas ang pinakamainam para sa aking MIG welding wire?
Ang shielding gas na pipiliin mo ay depende sa wire at sa application. Nagbibigay ang CO2 ng magandang penetration kapag nagwe-welding ng mas makapal na materyales, at magagamit mo ito sa mas manipis na mga materyales dahil mas malamig itong tumakbo, na nagpapababa sa panganib ng burn-through. Para sa mas maraming weld penetration at mataas na produktibidad, gumamit ng 75 percent argon/25 percent CO2 gas mix. Ang kumbinasyong ito ay gumagawa din ng mas kaunting spatter kaysa sa CO2 kaya mas kaunti ang post-weld cleanup.
Gumamit ng 100 porsiyentong CO2 shielding gas o isang 75 porsiyentong CO2/25 porsiyentong argon mix na pinagsama sa isang carbon steel solid wire. Ang aluminyo welding wire ay nangangailangan ng argon shielding gas, habang ang stainless steel wire ay pinakamahusay na gumagana sa isang tri-mix ng helium, argon at CO2. Palaging sumangguni sa spec sheet ng wire para sa mga rekomendasyon.
5. Ano ang pinakamahusay na paraan upang makontrol ang aking weld puddle?
Para sa lahat ng mga posisyon, pinakamahusay na panatilihing nakadirekta ang welding wire patungo sa nangungunang gilid ng weld puddle. Kung ikaw ay nagwe-welding sa labas ng posisyon (vertical, horizontal o overhead), ang pagpapanatiling maliit ang weld puddle ay nagbibigay ng pinakamahusay na kontrol. Gamitin din ang pinakamaliit na diameter ng wire na pupunuin pa rin ang weld joint nang sapat.
Maaari mong sukatin ang pagpasok ng init at bilis ng paglalakbay sa pamamagitan ng ginawang weld bead at ayusin ito nang naaayon upang makakuha ng mas mahusay na kontrol at mas mahusay na mga resulta. Halimbawa, kung gumawa ka ng weld bead na masyadong matangkad at payat, ito ay nagpapahiwatig na ang input ng init ay masyadong mababa at/o ang bilis ng iyong paglalakbay ay masyadong mabilis. Ang isang patag, malawak na butil ay nagmumungkahi ng masyadong mataas na input ng init at/o masyadong mabagal ng bilis ng paglalakbay. Ayusin ang iyong mga parameter at pamamaraan nang naaayon upang makamit ang perpektong weld, na may bahagyang korona na dumadampi lamang sa metal sa paligid nito.
Ang mga sagot na ito sa mga madalas itanong ay tumutukoy lamang sa ilan sa pinakamahuhusay na kagawian para sa MIG welding. Palaging sundin ang iyong mga pamamaraan ng hinang upang makakuha ng pinakamainam na resulta. Gayundin, maraming mga welding equipment at wire manufacturer ang may mga numero ng teknikal na suporta upang makipag-ugnayan sa mga tanong. Maaari silang magsilbi bilang isang mahusay na mapagkukunan para sa iyo.
Oras ng post: Ene-02-2023